DTF VS VINYL
Blog post description.
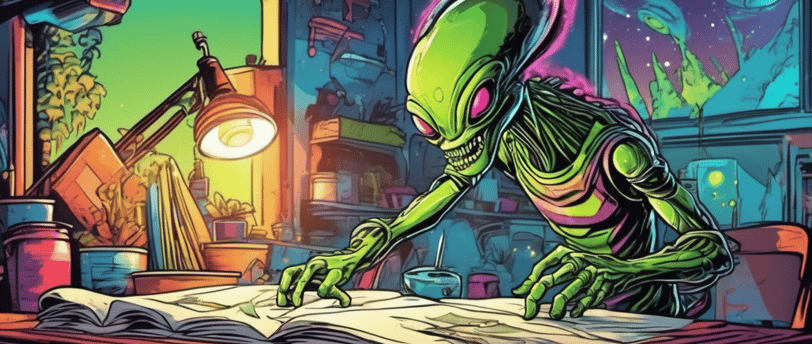
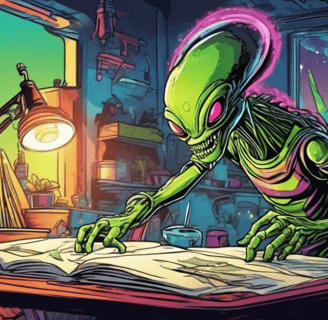
The Benefits of DTF Heat Transfers Compared to Vinyl Transfers
Introduction to DTF and Vinyl Transfers
Direct to Film (DTF) and vinyl transfers are two widely utilized methods in the apparel and merchandise industries for applying designs onto textiles. Each of these techniques offers its own unique properties and advantages, catering to varied applications and preferences among businesses and consumers.
DTF printing is a modern process that involves printing designs onto a special film, which is then transferred to the garment using heat and pressure. This method has gained popularity due to its versatility and ability to reproduce intricate designs with vibrant colors. DTF transfers allow for the decoration of a wide array of fabrics, ensuring durability and wash resistance, making them particularly suitable for custom apparel, promotional products, and small-batch production.
On the other hand, vinyl transfers rely on cutting specialized vinyl material to create designs, which are then heat-applied onto garments. This traditional method is often favored for simpler designs or logos, especially in the creation of sports jerseys, custom t-shirts, and promotional items where vivid colors and crisp lines are desired. While vinyl transfers can yield striking results, they may be limited when it comes to producing highly detailed images or complex color gradients.
Both DTF and vinyl transfers have carved their niches in the market, and their choice depends on various factors including the desired design complexity, the type of fabric, and production quantity. As we delve deeper into the benefits and considerations of each method, it becomes pertinent to understand how DTF’s innovative approach significantly contrasts with the more conventional vinyl transfer technique.
How DTF Heat Transfers Work
Direct to Film (DTF) heat transfer technology has emerged as a prominent method for applying designs onto various substrates. The process consists of several integral steps that contribute to its efficacy and versatility. Initially, the desired graphic or design is printed onto a specialized film using high-quality ink. This initial printing step is crucial as it determines the vibrancy and fidelity of the final output. The inks used in this process are typically water-based, offering an eco-friendly alternative without compromising on quality.
Once the design is printed, the next step involves applying an adhesive powder to the printed film. This adhesive is uniformly distributed over the wet ink, ensuring that the design will adhere effectively during the heat transfer process. The film is then subjected to a heat source, allowing the adhesive to bond with the ink, creating a durable layer that is ready for application.
The final step involves heat pressing the film onto the chosen substrate, such as T-shirts, hoodies, or other fabric items. A heat press machine is typically used for this purpose, allowing for precise control over temperature and pressure. During this stage, the film is positioned on the substrate, and heat and pressure are applied, activating the adhesive and allowing the design to transfer onto the fabric. The result is a high-quality design that is both vibrant and durable, capable of withstanding repeated washes without fading or peeling.
One of the significant advantages of DTF heat transfers is their versatility, allowing for application on various materials, ranging from cotton to polyester. This adaptability makes DTF a preferred choice for many businesses and hobbyists looking to create custom apparel. Additionally, the quality of DTF prints often surpasses that of vinyl transfers, offering rich colors and fine details that enhance the overall aesthetics of the finished product.
How Vinyl Transfers Work
Vinyl transfers have become a popular method for applying designs to various fabrics due to their ease of use and versatility. The process starts with a digital design that is created using graphic design software. This design is then transferred to a specialized vinyl cutter, which accurately cuts the design from a colored vinyl sheet. This cutter operates similarly to a printer, precisely slicing through the vinyl while leaving the backing intact.
Once the design is cut, the next crucial step is known as weeding. Weeding involves the careful removal of the excess vinyl surrounding the design, which typically requires patience and a steady hand. This process reveals the final shape of the design, eliminating any unwanted pieces and ensuring that only the intended elements remain. It’s essential for the quality of the final product, as mistakes during weeding can lead to incomplete or flawed designs.
With the design fully weeded, it is then prepared for heat application. A heat press is used to transfer the vinyl onto the fabric of choice. This step involves placing the weaved vinyl design on the desired area, followed by positioning a protective layer on top and applying heat and pressure. The heat causes the vinyl to adhere firmly to the fabric, creating a durable bond. This application process can vary in temperature and duration based on the specific vinyl and fabric types used.
While vinyl transfers offer numerous advantages, including vibrant colors and the ability for multi-layer designs, they do come with certain limitations. For example, intricate designs may become challenging to weed effectively, and the application process can be time-consuming for larger projects. Furthermore, vinyl transfers are not as breathable as some alternatives, potentially affecting the comfort of garments over time.
Cost-Effectiveness of DTF vs Vinyl Transfers
When considering the cost implications of DTF (Direct to Film) heat transfers versus vinyl transfers, several factors come into play that can significantly influence a business’s bottom line. An analysis of material costs indicates that DTF transfers often present a more economical choice, particularly when scaled for larger productions. The materials involved in DTF transfers, while slightly more expensive upfront, offer increased durability and versatility, which can translate into cost savings over time. Unlike vinyl, which may require multiple layers for complex designs, DTF allows for full-color printing in one application, reducing material waste and associated costs.
Moreover, labor time is a critical consideration when assessing cost-effectiveness. DTF heat transfers require less labor due to their straightforward application process. Once the design is printed onto the film, it can be heat applied directly onto the garment, streamlining production. In contrast, vinyl transfers necessitate precise weeding and layering, which can be labor-intensive and time-consuming. The real-time saved by opting for DTF transfers can therefore contribute significantly to overall labor cost reduction, particularly for businesses processing large orders.
Production scale further enhances the financial benefits associated with DTF transfers. As production volumes grow, the capacity for quicker outputs with less wasted material makes DTF an attractive option. Businesses that utilize DTF can benefit from bulk purchasing of materials, resulting in lower per-unit costs. This efficiency can lead to more competitive pricing strategies and higher profit margins in the long run.
In conclusion, the cost-effectiveness of DTF heat transfers, particularly when compared to vinyl transfers, is evident in their material savings, reduced labor time, and scalability. These factors collectively contribute to more financially viable operations for businesses engaged in garment printing, making DTF a compelling choice for those looking to optimize their production processes.
Quality of Prints: DTF vs Vinyl
When evaluating the quality of prints produced by DTF (Direct to Film) heat transfers and vinyl transfers, several critical factors come into play, including color vibrancy, detail, image longevity, and texture. Each printing method has its unique strengths that influence the overall aesthetic and functional quality of the final product.
In terms of color vibrancy, DTF heat transfers exhibit a broader color gamut than vinyl transfers, allowing for the reproduction of intricate designs with vivid hues. This is primarily due to the advanced ink technology used in DTF processes, which enables a rich palette and smoother gradients. In contrast, vinyl transfers are often limited to predefined color options, which may restrict the artist’s vision and result in less dynamic outputs.
Detail is another area where DTF shines. The DTF printing technique captures fine details exceptionally well, making it suitable for designs that incorporate complex imagery or small text. Vinyl transfers, while capable of producing sharp images, may struggle with fine details, especially on smaller items or those requiring intricate patterns. This difference can significantly affect the overall quality, particularly in high-resolution designs.
Regarding image longevity, DTF prints tend to adhere better to various fabrics, ensuring that the vibrancy of the design persists even after multiple washes. On the other hand, vinyl transfers can fade or crack over time, compromising the longevity of the print. As for texture, DTF prints typically offer a softer finish as they become part of the fabric, while vinyl can present a thick, raised texture that may not be suitable for all applications.
In summary, DTF heat transfers provide superior color vibrancy and detail, alongside better longevity and a generally softer texture than vinyl transfers. These factors make DTF a compelling choice for designers aiming for high-quality apparel and intricate designs.
Durability and Washability Comparison
When comparing DTF (Direct to Film) heat transfers and vinyl transfers, one of the most significant factors to consider is durability and washability. Both methods are prevalent in the custom apparel industry, yet they exhibit distinct characteristics that influence their longevity on garments. DTF heat transfers have gained popularity due to their remarkable resilience. These transfers are printed with high-quality inks that bond well with the fabric, ensuring that designs maintain their vibrancy and integrity even after multiple washes. In laboratory tests, DTF prints have been shown to withstand more than 50 washes without noticeable fading or cracking, making them an excellent choice for garments expected to endure frequent cleaning.
On the other hand, vinyl transfers are made from a polymer or polyurethane film, which is cut out and then heat pressed onto the fabric. While vinyl can provide a crisp and vibrant finish, its durability can be somewhat compromised when compared to DTF. Over time, vinyl transfers may exhibit cracking or peeling, particularly when subjected to frequent washes. Factors such as the quality of the vinyl used and the care instructions provided influence their overall lifespan. Generally, vinyl transfers are more susceptible to wear, especially in high-friction areas such as the sides of shirts or around the neckline.
Furthermore, the washability of each transfer method can be influenced by the fabric type. DTF works effectively on various materials, including cotton, polyester, and blends, whereas vinyl is typically more limited in its application. While some brands of vinyl are designed for high-performance textiles, they may not offer the same versatility as DTF. Therefore, when it comes to evaluating durability and washability, DTF heat transfers often present an advantage, particularly for products that are meant to endure wear and tear over time.
Color Range and Design Flexibility
In the realm of textile printing, the choice of transfer method can significantly influence the outcome in terms of color range and design flexibility. DTF (Direct-to-Film) heat transfers have revolutionized this area by permitting a broader spectrum of colors and more intricate designs compared to traditional vinyl transfers. DTF technology enables the printing of high-resolution, full-color graphics, which means that complex images, multi-color logos, and photographic designs can be effortlessly transferred onto garments.
One of the distinguishing advantages of DTF over vinyl transfers is its ability to reproduce hues with precision and richness. While vinyl transfers are often restricted to a limited color palette, making it challenging to create gradients or elaborate designs, DTF allows for a virtually unlimited range of colors. This is particularly beneficial for businesses aiming for brand consistency, as they can replicate specific brand colors without compromising on quality. Furthermore, the printing process of DTF involves using specialized inks that integrate seamlessly with various fabrics, resulting in vibrant prints that maintain their brilliance over time.
Another aspect worth mentioning is design flexibility. DTF transfers can handle intricate patterns and detailed artwork with ease, accommodating small text, fine lines, and delicate visuals that might be difficult or impossible to achieve with vinyl. This capability makes DTF ideal for custom apparel and unique merchandising opportunities where individual expression is paramount. On the other hand, vinyl transfers may require simplification of designs, limiting creativity and potentially resulting in less captivating products.
Overall, when evaluating options for heat transfer applications, the advantages of DTF heat transfers in terms of color variety and design adaptability are significant, making them the preferred choice for many professionals in the apparel industry.
Environmental Considerations
When evaluating the environmental considerations of DTF (Direct to Film) heat transfers versus vinyl transfers, a variety of factors must be taken into account, including ink formulations, production processes, and waste management practices. DTF heat transfer technology uses special inks that are often water-based, which in general pose less harm to the environment compared to the solvent-based inks typically used in vinyl transfers. Water-based inks reduce the emission of volatile organic compounds (VOCs), which are harmful chemicals that can contribute to air pollution and have been linked to various health issues.
The production process is another crucial determining factor for sustainability. DTF transfers generally require less energy and fewer resources than vinyl methods. The DTF process involves printing designs on a special film, which can be subsequently transferred onto fabrics using a heat press. This direct application results in less material waste as compared to the vinyl process that necessitates the cutting and weeding of excess material. Moreover, the ability to print intricate designs directly onto the film without the need for multiple layers helps to minimize waste generation.
In terms of waste management, DTF heat transfers can potentially align better with sustainable practices due to their lower material input and the possibility of utilizing recyclable transfer films. On the other hand, vinyl transfers often contribute to synthetic waste, which can take a significant time to decompose. The challenge lies in the disposal of vinyl materials, as many vinyl products do not break down naturally in the environment and can result in long-term pollution. Therefore, from an environmental standpoint, DTF heat transfers emerge as a more sustainable alternative, combining reduced chemical usage with a lower overall ecological footprint.
Conclusion: Which Method to Choose?
In evaluating DTF heat transfers and vinyl transfers, it becomes clear that both techniques offer unique advantages suited to different applications. DTF heat transfers stand out for their vibrant color reproduction and intricate designs. They allow for precise detailing, making them ideal for complex graphics. This method is particularly beneficial for businesses looking to produce designs that have a photographic quality or require a diverse palette, as DTF transfers can handle a wider spectrum of colors without compromising the design integrity. Moreover, the application process for DTF can be simpler and quicker, streamlining production for bulk orders.
On the other hand, vinyl transfers are known for their durability and long-lasting results. They generally resist wear and tear better than other methods, making them a preferable choice for apparel that sees frequent washing and use. Vinyl is excellent for simpler designs or text, where clarity and longevity are critical. Businesses prioritizing durability with straightforward graphics may find vinyl transfers to be the more advantageous option. Additionally, the cost-effectiveness of vinyl transfers for smaller runs cannot be overlooked, as they often require less upfront investment in materials compared to DTF.
When deciding between the two methods, consider your specific project needs. If your priority lies in producing vibrant, intricate designs, DTF heat transfers may be the optimal choice. Conversely, for projects emphasizing durability and simplicity, vinyl transfers would be more suitable. Ultimately, the decision should align with the business objectives, target audience, and the intended lifespan of the printed products, ensuring that the chosen transfer method meets both aesthetic and practical requirements efficiently.